Custom Powder Metal Services

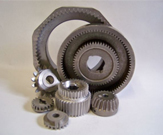
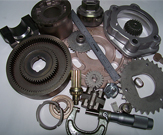
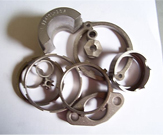
[click to enlarge]
Advantages of the PM process:
Ridgway Powdered Metals, Inc. is a true pioneer in this industry having aggressively invested in the technology and equipment which allows it to take full advantage of its many benefits.
Among PM's advantages are:
- Eliminates or minimizes machining by producing parts at - or close to - net shape
- Eliminates or minimizes scrap losses by typically using more than 97% of the starting raw material in the finished part
- Permits a wide variety of alloy systems – some brand-new, others RPM proprietary grades – for customers' items.
- Produces good surface finish – 32 RMS or better
- Provides heat-treatable materials for increased strength, wear resistance and durability
- Provides controlled porosity for self-lubrication or filtration
- Facilitates manufacture of complex or unique shapes which would be impractical or impossible with other metalworking processes
- Is suited to moderate to high volume component production requirements
- Offers long-term performance reliability in critical applications
- Is a "GREEN" and SUSTAINABLE industry
- Is cost-effective - minimal average cost advantage is 30% (others more than 100%) over other metal working technologies
Our modern facilities list includes:
- 30 presses whose compacting forces range from 4 through 550 tons, and whose large presses include 5 level capabilities
- Sintering furnaces – both conventional and high-temperature units – with large volume production capacities and precise controls for each application
- Ancillary deburring, impregnation and other secondary apparatus are on hand and available for customers' critical applications.
- RPM manufactures parts measuring from 0.06"to 4.0" long with diameters from 0.25" to 6.0" and weights from a few grams up to 8 lbs.
- RPM consistently achieves net shape tolerances as low as ± .0003" on horizontal surfaces
- Production rates are rapid at RPM, and dimensional integrity is maintained from part to part, order to order.
- Applications are almost limitless, and prices are very reasonable.
Contact Us today to learn how our custom powder components can provide a cost effective option for your next project.
Materials:
RPM builds parts in all of the standard Metal Powder Industries Federation (MPIF) grades as well as RPM proprietary grades. (Information by request)
(See "Materials Standards for PM STRUCTURAL PARTS", and "Materials Standards for SELF-LUBRICATING BEARINGS" MPIF Standard 35)
Listed below are some of the more common grades and their possible applications:
(It is recommended that you discuss material selection with RPM Engineering prior to specifying one for your application.)
- Material
- MPIF CODE
- Characteristics
- Iron
- F-0000
- Electro-Magnets
- Iron/Carbon
- F-0003/F-0008
- Moderate Strength, Heat treatable
- Iron/Copper/Carbon
- FC-0200 to FC-0208
- Good strength and wear resistance, Heat treatable
- Iron/Nickel/Carbon
- FN-0200 to FN-0408
- Good impact strength and wear properties, Heat treatable
- Alloy Steels
- FLN2C-4005 to FLDN4C2-4905
- A wide variety of materials with specific properties to match the critical requirements of the application – all are Heat treatable
- Copper Infiltrated Steel
- FX-1005 to FX-2008
- Good strength, improved machinability, gas tight Heat treatable
- Stainless Steel
- SS-303, SS-304, SS-316, SS-409,
SS-410, SS-430, SS-434, 17-4PH - Select the stainless grade that will satisfy your requirements for corrosion resistance, ductility, machinability, etc.
- Copper
- C-0000
- Electrical applications
- Bronze
- CT-1000
- Self-Lubricating Bearings
- Brass
- CZ-1000, CZ-2000
- Mechanical components and Hardware
Tolerances
Below are shown the typical tolerances for PM parts having uniform cross-sections.
- Characteristic
- As Sintered
- Decimal
- Metric
- As Sized or Coined
- Decimal
- Metric
- Length
Inside Diameter
Outside Diameter
Concentricity
Flatness
Parallelism
Perpendicularity -
- ± 0.005"
± 0.002"
± 0.002"
0.003
0.002
0.002
0.002 - ±0.126
±0.051
±0.051
0.076
0.051
0.051
0.051
- ± 0.005"
-
- ± 0.002"
± 0.0003"
± 0.001"
0.003
0.002
0.002
0.002 - ±0.051
±0.008
±0.0025
0.076
0.051
0.051
0.051
- ± 0.002"
Some dimensional and feature tolerances may be reduced with secondary machining and grinding operations.
Discuss those possibilities with RPM Engineering.
Industries served
- Automotive
- The largest market for PM parts
- Home Appliances
- Virtually every appliance in use today contains some PM parts
- Power Tools
- PM parts have helped to make them available and inexpensive
- Fluid Power
- High-density and copper infiltration produce pressure retaining components
- Lawn & Garden
- That lawn mower, hedge clipper and others are full of PM parts
- Agriculture
- See that big green or yellow or orange machine in the grain fields - they are all using many PM parts
- Construction
- Even the mighty bull-dozer must rely on certain PM parts
- Motors
- Self-lubricating bearings and PM magnets (electro and permanent) keep the motors running
- Off-Road
- Both for utility and sport
- Recreation
- Fishing reels and skate boards, outboard motors and bicycles, guns and golf clubs, and many more use PM parts
- Hardware
- Fasteners, washers, bushings, connectors, spacers, and all sorts of necessary products
- Business
- Computers, shredders, printers, recorders, fax machines happily find PM parts just what they need
- Vending
- Multiple applications
- Conveyors
- Rollers, cams, sprockets, gears
- Materials handling
- Connectors, latches, fingers, catches, pushers and many more
- Miscellaneous
- Exercise apparatus, cutter blades, gas filters, weapons, munitions, etc., etc., etc.
Design considerations
Many features that are found on parts made with other metal working techniques are there due to how they were built. PM usually can eliminate them.
PM parts can be produced with great geometric complexities. There are feature considerations, somewhat unique with PM, that should be avoided. Some are listed below.
- No feature that would resist ejecting parts from tools: reverse tapers, holes other than in the direction of pressing, threads, undercuts, diamond knurls (all of these can be included using secondary machining)
- Thin walls, narrow splines, fine pitch gears (finer than 48 pitch) and sharp corners should be avoided
- Features that require very delicate tools to compact – due to the very high compressive forces needed to compact metal powders.
- Vertical lengths not to exceed ratios of 4 to 1 of their horizontal ones on heavy-walled objects; 2 to 1 on thin-walled ones
- Knife or feather edges should be designed out of parts
- Small projections on top faces of parts need to be large enough to allow for tool safety, ease of ejection, and be located inboard from outside edges of parts.
It is always good practice to discuss your parts – those having questionable features – with RPM Engineering.
Virtually any feature that would create problems or be impossible to compact with hard compacting tooling can be added using machining operations.
Whenever a part can be modified to eliminate the additional secondary operations its price will obviously be more advantageous.
Contact Us today to learn how our custom powder components can provide a cost effective option for your next project.